Key messages:
- 2023 to 2024 saw Network Rail maintain good performance but facing continuing challenges with managing asset safety in the face of weather-related risks, especially from extreme weather. Although still being implemented, Network Rail’s Modernising Maintenance reforms have the potential to deliver efficiencies but need to be done in a way that does not overload people with too much change too quickly, nor result in fatigue. Network Rail has delivered effective change safely through trackworker safety reforms. It needs to do more to embed the changes through sustainable ways of working that allow maintainers the track access they need as it continues its reorganisation of maintenance work.Â
- Network Rail needs to maintain its focus on providing a safe and resilient railway as it enters Control Period 7. It needs to prioritise its people and their capability to maintain the safety of the network as it continues to implement maintenance reforms, and it needs to continue to deliver effective improvements to trackworker safety by embedding sustainable change.Â
Network Rail’s management maturity
RM3 assessment of Network Rail’s management maturity is based on the evidence we gather from our inspections and other regulatory work. It offers an objective, independent view of maturity. This year we assessed 22 (out of 26) elements. Last year we assessed 3 elements at ‘managed’ and 18 at ‘standardised’. This year we assessed 1 at ‘predictable’, 7 at ‘managed’ and 14 at ‘standardised’.
Figure 1: Network Rail 2023 to 2024 RM3 Assessment
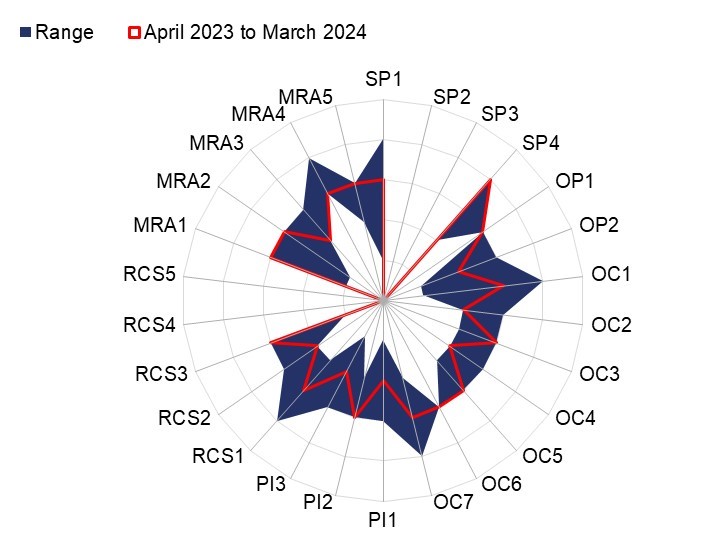
Source: ORR
Table 1: Network Rail 2023 to 2024 RM3 Assessment
Code | Description | 2023 to 2024 Assessed Level | Min | Max |
---|---|---|---|---|
SP1 | Leadership | 3 | 1 | 4 |
SP2 | Health and Safety Policy | Not Assessed | n/a | n/a |
SP3 | Board Governance | Not Assessed | n/a | n/a |
SP4 | Written Safety Management System | 4 | 2 | 4 |
OC1 | Allocation of Responsibilities | 3 | 1 | 4 |
OC2 | Management and Supervisory Accountability | 2 | 2 | 3 |
OC3 | Organisational Structure | 3 | 2 | 3 |
OC4 | Internal Communication Arrangements | 2 | 2 | 3 |
OC5 | System Safety and Interface Arrangements | 3 | 2 | 3 |
OC6 | Organisational Culture | 3 | n/a | n/a |
OC7 | Record Keeping, Document Control, and Knowledge Management | 3 | 2 | 4 |
OP1 | Worker Involvement and Internal Co-operation | 3 | 3 | 3 |
OP2 | Competence Management System | 2 | 1 | 3 |
PI1 | Risk Assessment and Management | 2 | 1 | 3 |
PI2 | Objective and Target Setting | 3 | 2 | 3 |
PI3 | Workload Planning | 2 | 1 | 3 |
RSC1 | Safe Systems of Work Including Safety Critical Work | 3 | 2 | 4 |
RSC2 | Management of Assets | 2 | 2 | 3 |
RSC3 | Change Management (Operational, Process, Organisational, and Engineering) | 3 | 1 | 3 |
RSC4 | Control of Contractors and Suppliers | Not Assessed | n/a | n/a |
RSC5 | Emergency Planning | Not Assessed | n/a | n/a |
MRA1 | Proactive Monitoring Arrangements | 3 | 1 | 3 |
MRA2 | Audit | 3 | 1 | 3 |
MRA3 | Incident Investigation | 2 | 2 | 3 |
MRA4 | Management Review | 3 | 3 | 4 |
MRA5 | Corrective Action | 3 | 2 | 3 |
Source: ORR
Our overall assessment is that Network Rail is at the ‘standardised’ level of management maturity. This is the same as last year’s assessment. However, this year, we found less consistency. We assessed more criteria at ‘managed’ than last year. This might suggest a lessening of overall management maturity. Our evidence is drawn from our inspections and investigations which, of necessity, tend to highlight known weaker areas. Nevertheless, compared to last year’s assessment which focused similarly on weaker areas, the consistency of maturity appears diminished.
Our overall perception is unchanged from last year; the degree of leadership on a given topic or risk does much to determine overall attainment. Whilst Network Rail has many processes, procedures and standards to manage risks, it manages those best where leaders give their attention.
Without this attention, Network Rail can be slow to achieve commitments necessary to bring them into legal compliance. We found this was the case with reducing earthworks and structures inspections backlogs, and the completion of drainage asset surveys. Both these matters have taken and continue to take much time and effort on our part to secure improvements. Recognising, accepting, and delivering robust action where basic requirements are not being met would show a mature approach to safety management that does not accept as ‘business as usual’ long term non-compliance with standards. Network Rail needs to apply leadership focus to proactively ensure that its own standards are being met across the network.
Risk performance
There were 33 train accident risk high potential incidents this year, significantly more than the 20 incidents in 2022 to 2023. (All figures from Network Rail Safety, Health & Environment Performance (SHEP) Report, 2023-24 period 13). Although higher this year, the number is in line with fluctuations seen in the past, and often related to poor or extreme weather. Near misses or glancing collisions with road vehicles at level crossings feature most prominently, followed by signals passed at danger (SPADs) with potentially high consequences, then trains passing over or near debris from earthworks and bridge failures or passing over unsupported track from embankment failures. Other failures comprised risks from faulty, speeding and runaway trains and striking fallen trees.
The Rail Safety and Standards Board (RSSB) Precursor Indicator Model (PIM) is the way Network Rail measures failures that have the potential to result in a catastrophic accident. Looking back over Control Period 6 (the last 5-year funding period between 2019 to 2024), the trend in overall precursor risks was dominated by variations in earthworks failures, especially between 2020 to 2022, largely related to adverse weather conditions, as well as an increase in SPAD and adhesion events. These trends were partly offset by a reduction in level crossing risk and objects on the line. Numbers of other risk events were broadly static across the control period. Comparing the start and end of the control period, the level of precursor risk remained largely unchanged. (PIM chart generated from RSSB website tool on 10 April 2024, latest data at time of writing.)
Figure 2: Precursor Indicator Model (PIM)
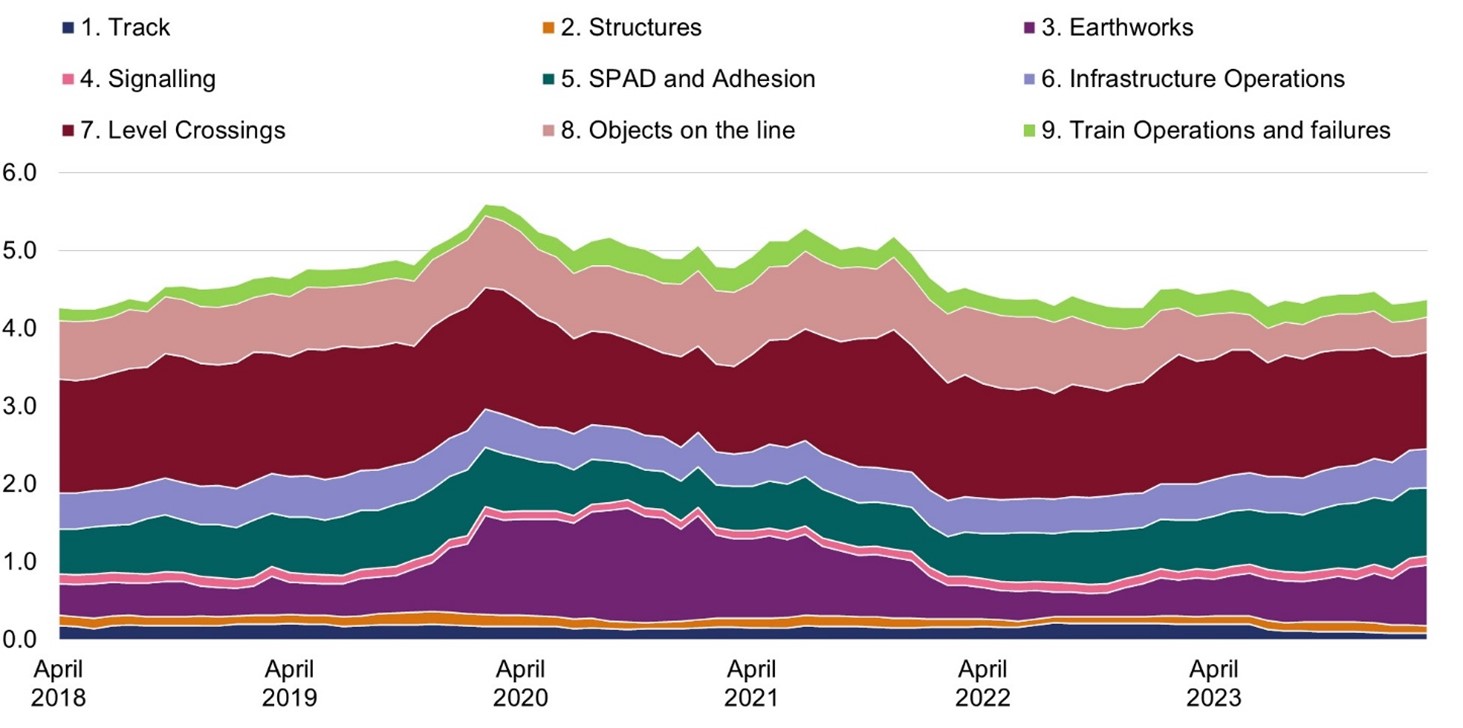
Source: RSSB
 In 2023-24 the overall level of precursor risk was similarly largely unchanged. Earthworks failures increased towards the end of the year, and SPAD and adhesion risk rose steadily throughout the year. These rises were offset by prolonged reductions in risk from level crossings and objects on the line. (Data and chart generated from RSSB website tool on 11/4/2024).
Occupational Health and Safety performance
Network Rail’s occupational health and safety performance was broadly neutral in 2023 to 2024. The fatality weighted index (FWI), a measure of accident severity, improved slightly in the year. Network Rail’s long-term injury frequency rate (LTIFR) increased very slightly over the year. Most accidents are caused by slips, trips and low falls.
There were 19 workforce safety high-potential incidents in 2023 to 2024. By far the largest single cause involved near-misses to track or trackside workers in line blockages, or associated line blockage irregularities. It shows a substantial reduction from 29 incidents in 2018-19, immediately before ORR’s enforcement action requiring improvements to track worker safety.
Occupational health achievement continues to be positive in some important areas. Following difficulties achieving compliant timescales for hand-arm vibration (HAVS) health surveillance, Network Rail is achieving good compliance rates, at or near 100%. In part this might explain why numbers of HAVS cases have risen substantially from 15 cases in 2022 to 2023, to 23 this year. We also support the continued work to provide occupational health clinics to the workforce. Â
Asset safety
The current rate of high-consequence earthworks failures is at its highest since the inception of this metric in 2008 (graph supplied by Network Rail). Failures are closely related to poor and extreme weather, especially high rainfall. The failures illustrate the importance of good drainage asset knowledge and effective inspection and maintenance regimes.
That there have been no derailments as a consequence of earthwork failure shows the importance of managing the consequences of failure through remote and on-site monitoring, as well as forecasting and speed restrictions, subjects we continue to pursue through our inspection activity.Â
Graphs showing annual potentially high consequence earthworks failures and annual derailment rate. Potentially high consequence failures are those scoring 50 and above based on the CIV/185 standard.
Figure 3a: High consequence earthworks failuresÂ
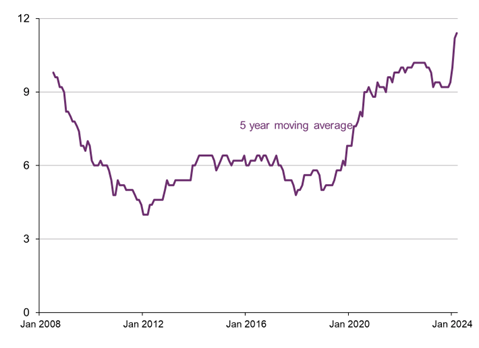
Source: Network Rail
Figure 3b: Annual derailment rates
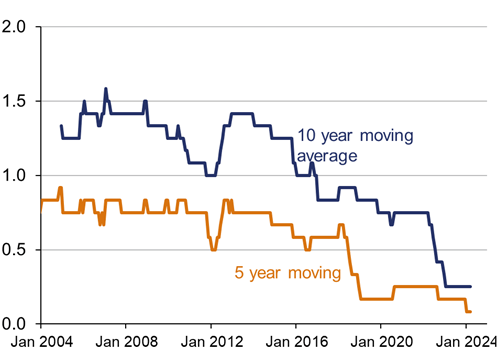
Source: Network Rail
Throughout 2023 to 2024 we continued to challenge Network Rail to improve its knowledge of drainage assets and systems, and to establish adequate inspection and maintenance resource levels. These priorities were partly in response to recommendations made by Lord Mair and Dame Julia Slingo following the Carmont derailment in 2020, but also reflected our longstanding concerns around earthworks and structures resilience in the face of increasing numbers and intensities of extreme weather events. Having an accurate picture of the nature and location of drainage, and having sufficient people to maintain it, are both essential prerequisites to an effective maintenance and inspection regime and thus effective drainage.
In 2020 to 2021 Network Rail committed to completing drainage asset survey reviews by the end of March 2024. 3 regions met this deadline but 2 – Southern and Eastern - did not. However, they both provided credible plans to complete the work by the end of May and October respectively which we continue to monitor to completion. North West and Central and Scotland regions met their targets for providing sufficient resources to carry out drainage inspections and maintenance by employing external contractors. The remaining 3 regions continue to recruit staff, using contractors in the interim.Â
The resources that have been provided are not necessarily dedicated resources, the original intent of the Mair recommendation. We look forward to Network Rail completing its asset surveys and demonstrating delivery of effective drainage maintenance and inspection using non-dedicated staff and sub-contract labour. We will continue to engage with Network Rail on this topic.
We obtained clarity from Network Rail on progress towards implementation of the Mair/Slingo recommendations by the Weather Risk Task Force (WRTF). Our visibility of progress is much improved. At the time of writing Network Rail has implemented nationally four of the 18 Mair recommendation related action plans, focused on updating Network Rail’s policy and controls, and modelling surface water threats. A further 6 action plans, focused on practical improvements to drainage and earthworks management, and the establishment of Slope Safety Review Groups, have been implemented in at least one Region. Â
One of the 5 Slingo action plans, on exploiting advances in forecasting to improve operational safety and performance, has also been implemented centrally. We engaged with Network Rail on PRIMA (Proportionate Risk Response to Implementing Mitigating Speeds to Assets), a programme that aims to balance the need to reduce the consequences of extreme weather through speed restrictions, with maintaining train performance to minimise disruption and inconvenience to passengers. PRIMA is being trialled and we await results to demonstrate it will deliver sufficient levels of safety, and whether PRIMA will drive decisions or be a decision support tool sitting alongside local knowledge. We will continue to monitor developments in this area.
Network Rail struggles to deliver enough earthworks and structures examinations. Nationally, structures examinations compliance has not improved significantly on last year, although there are significant regional variations. For earthworks examinations, although improving from last year, backlogs remain above historic levels. Regular examinations are essential to ensuring the continued safety of structures and earthworks and we continue to monitor progress towards improvements in this area.
Track and lineside
The safety of the track continues to be well managed through inspection and maintenance activity. However, it is vulnerable to human failings. Safety is dependent on an inspection, maintenance and corrective action regime that relies on competent people following the standards - doing the right things, in the right way, at the right time. Our investigation into a rail break at Colton Junction on East Coast route in May 2023 shows that without effective leadership, adequate resourcing and robust monitoring, track integrity can be seriously compromised. Track integrity also relies on the inspection and maintenance regime evolving over time as train tonnages increase and as new rolling stock is introduced. We continue to explore these areas with Network Rail to ensure that the lessons from incidents such as rail breaks, are fully learned.
The year saw a number of collisions with fallen trees, brought down by high winds (e.g. Broughty Ferry, December 2023, Thetford, February 2024). Though the potential was present, none of these resulted in serious incidents or injury. Positively, Network Rail has made efforts to map vegetation and identify potentially falling trees and we continue to look for progress in this area. We recognise this is a challenging topic. Whilst judgement and analysis go so far, there remains the unpredictable element of hidden weakness or loose soil. Another challenge is dealing with trees on neighbouring land. Â
Trackworker safety
Following our enforcement action in 2019, and Network Rail’s improvements to trackworker safety, we carried out a series of inspections across the network. These inspections were aimed at gaining insight into the work being done to embed long-lasting, sustainable changes in culture and working practices around track access for maintenance, and how Network Rail has continued to drive further change and innovation. Positively, we found that the routes were consistent in their dedication to embedding safer working practices and driving continued improvements, and generally open to engaging with and learning from other areas of the organisation and the wider industry.
The pursuit of flexible, efficient technological and procedural solutions appears to be strong, with numerous trials planned or active across the network. In the meantime, access to and use of additional protection (AP) in line blockages has been gradually increasing, though securing improvements has been challenging. The introduction of equipment to protect workers from, or warn them about approaching trains, such as remote track circuit operating devices (remote T-CODs) and semi-automatic track warning systems (SATWS) has been particularly fraught, with significant delays and concerns around reliability, performance, and placement. Network Rail needs to do more to maximise the potential of available technology.
Although there were no accidents, near-misses continued to happen. The main causes were (1) trains mistakenly signalled into line blockages, and (2) workers on open lines but believing themselves to be in a possession or line blockage. The next 5 years will require Network Rail to identify and adopt solutions to provide more efficient track access which delivers the time and quality of access to maintain the network. This will require improvements to trackworker safety technology and procedures to facilitate more efficient access, particularly better AP and train warning systems, whilst maintaining the cultural shift.
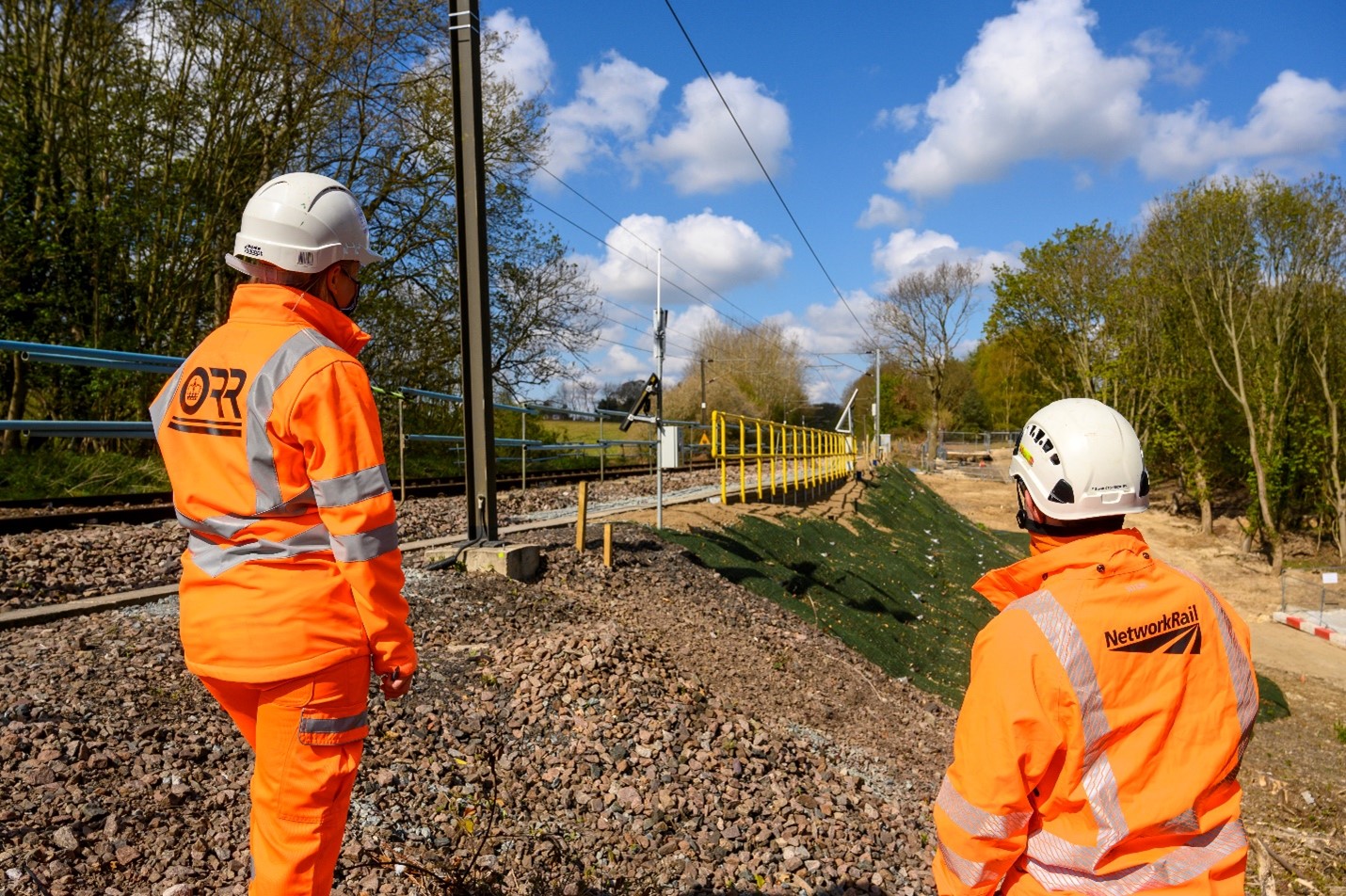
Modernising maintenance
We engaged centrally and at route level with Network Rail as they planned for, and introduced, Modernising Maintenance. This initiative aims to maximise use of maintenance resource through re-setting resource levels, eliminating unnecessary maintenance work, and changing working patterns. Like all changes to safety-critical maintenance work there is the risk that, if done in a rushed or poorly managed way, essential maintenance work could be done badly, or not at all.Â
We inspected the introduction of Modernising Maintenance in 4 routes, focusing particularly on the ability to maintain a safe railway, consultation with trades unions safety representatives, how specific route challenges are identified and addressed, and whether maintenance resourcing is robustly assessed and maintained at appropriate levels. Â
Overall, we found a sensible and mature approach to managing change. A robust change management process identified national and local risks and ensured that these were appropriately considered. We also found that safety representatives were appropriately consulted on the changes. Less positively, in some places we found a maintenance organisation that faced challenges delivering all that is required, with high levels of backlogs and deferrals of scheduled work, staff working long hours, and fewer staff to call on. It is too early to know whether Modernising Maintenance will deliver all that it promises.Â
At the moment, we believe that Network Rail has the processes and standards in place that if properly implemented will identify and control the risks of any shortcomings in the effectiveness of maintenance work that might arise as an unintended consequence of the changes. We will continue to monitor this major change to established ways of working through further inspections, planned for 2024 to 2025.
Electrical safety
We continued to monitor progress made against commitments in the Electrical Safety Delivery (ESD) program. Network Rail progressed the deployment of the negative short-circuiting devices and track circuit switches in conductor rail areas that has eliminated the need to use 34,000 earthing straps over the past 5 years. The plan is to have 80% coverage across the 3rd rail network by the end of 2029. Work continues on the development of remote securing of isolations, an improvement that promises better safety and more time for maintenance work on track. This roll out is dependent on the successful introduction of the delayed Traction Power Control Management System (TPCMS).
Following our enforcement action in 2021 concerning safety in demarcating overhead line equipment (OLE) isolations and ensuring electrical equipment was dead before working, we assessed Network Rail’s continuing work to assure themselves that the new procedures they introduced were being followed. This work was carried out across all regions with inspectors carrying out joint work with Network Rail and their contractors. We found a positive picture of continued embedding of significant improvements in this area.
Human factors
Following Network Rail’s reduction in in-house human factors expertise in previous years, we continue to have concerns about the ability of its suppliers to robustly assess and mitigate risks associated with human factors. Shortcomings in this area can have long-standing and unforeseen consequences if the human interface is not optimised when new equipment is introduced. We remain concerned that Network Rail lacks the capacity to challenge suppliers to deliver good human factors work, and we continue to press for a more proactive, better resourced approach to this topic. This includes meeting with the Network Rail Human Factors Lead on a quarterly basis to understand their current priorities and approach.
Fatigue
Throughout the year we have been concerned at high numbers of fatigue exceedances, where Network Rail staff worked longer hours than allowed by their own standards. We welcomed positive developments such as fatigue risk training for maintenance rostering clerks and resource managers, as well as recent improvements in using fatigue assessments and fatigue management plans to ensure that, where people need to work longer hours, the risks are assessed, and appropriate mitigations put in place. These measures reflect some effort made to raise awareness of fatigue risks within Network Rail. We recognise that reducing exceedances and managing fatigue risk is a complex task that will require addressing established ways of working, staff retention issues and industrial relations matters. However, Network Rail should continue to move towards the standards set out in good practice guidance and ensure that their own internal standards are aligned.
Level crossings
Tragically there was 1 accidental fatality in 2023 to 2024, at Pooley Green crossing in Surrey in October 2023. This compares to 5 accidental fatalities in 2022 to 2023 and 7 in 2021 to 2022. Near-misses declined from a peak in the early part of 2023 to 2024. Overall, there were 426 near misses with pedestrians and 56 near misses with road vehicles in 2023 to 2024.Â
Although undoubtedly related to wider societal factors, the reduction probably also reflects Network Rail’s efforts at educating users and raising awareness. Although the overall trend is positive, near-misses with pedestrians continue to rise at footpath crossings. This maintains a trend since 2020. Positively, we noted Network Rail’s continued development of technology, as well as exploring ways of reducing the cost of existing technology, to provide better warning at footpath and user worked crossings.
Overall risk from level crossings, as measured by Network Rail’s All Level Crossing Risk Model (ALCRM) reduced very slightly in 2023 to 2024, probably reflecting that there are fewer ‘easy wins’ still available in the form of level crossing closures or potential for upgrading risk controls at crossings. (National SHEP 2023 to 2024 P13)
Our focus this year continued themes from previous years, in particular monitoring delivery of Network Rail’s ‘Enhancing level crossings safety strategy 2019-2029’. In this context we noted positive engagement on revising signage at private crossings and devising and rolling out ‘another train coming’ signs.
Occupational health
We have been focusing our occupational health regulation at Network Rail on the risks arising from welding fume. This work started a number of years ago with our interest in the control of weld fume increasing following the issue of a Safety Alert by the Health and Safety Executive in February 2019 setting out the new evidence that all types of welding fume can cause lung cancer and limited evidence pointing to a link with kidney cancer.Â
This work has seen us challenge Network Rail on their approach to the assessment of welding fume and the application of the hierarchy of risk control to its welding operations. We found disappointing progress and have been challenging Network Rail to assess risks robustly and implement suitable and sufficient control measures in line with other industries, rather than placing a reliance on lower-level controls such as respiratory protective equipment.
Operations
We continue to note and investigate events where trains have exceeded maximum permanent or temporary speed limits, for example at Wood Green and Melton Lane level crossing, in June 2023.Â
Generally, there is a lack of data on the nature and prevalence of these events, with the suspicion that these events are grossly under-reported. Modern trains also accelerate more quickly and quietly than older trains. We also note a continued rise in signals passed at danger (SPAD’s), especially involving empty coaching stock and freight movements.
For these reasons we welcome Network Rail’s Control Period 7 business plan commitment to explore a driver speed advisory system that would give the driver real-time speed limit and exceedance information as well as automatic over-speed braking. Overall, Network Rail needs to be working to secure a settled, industry-wide approach to future train protection and speed supervision.Â
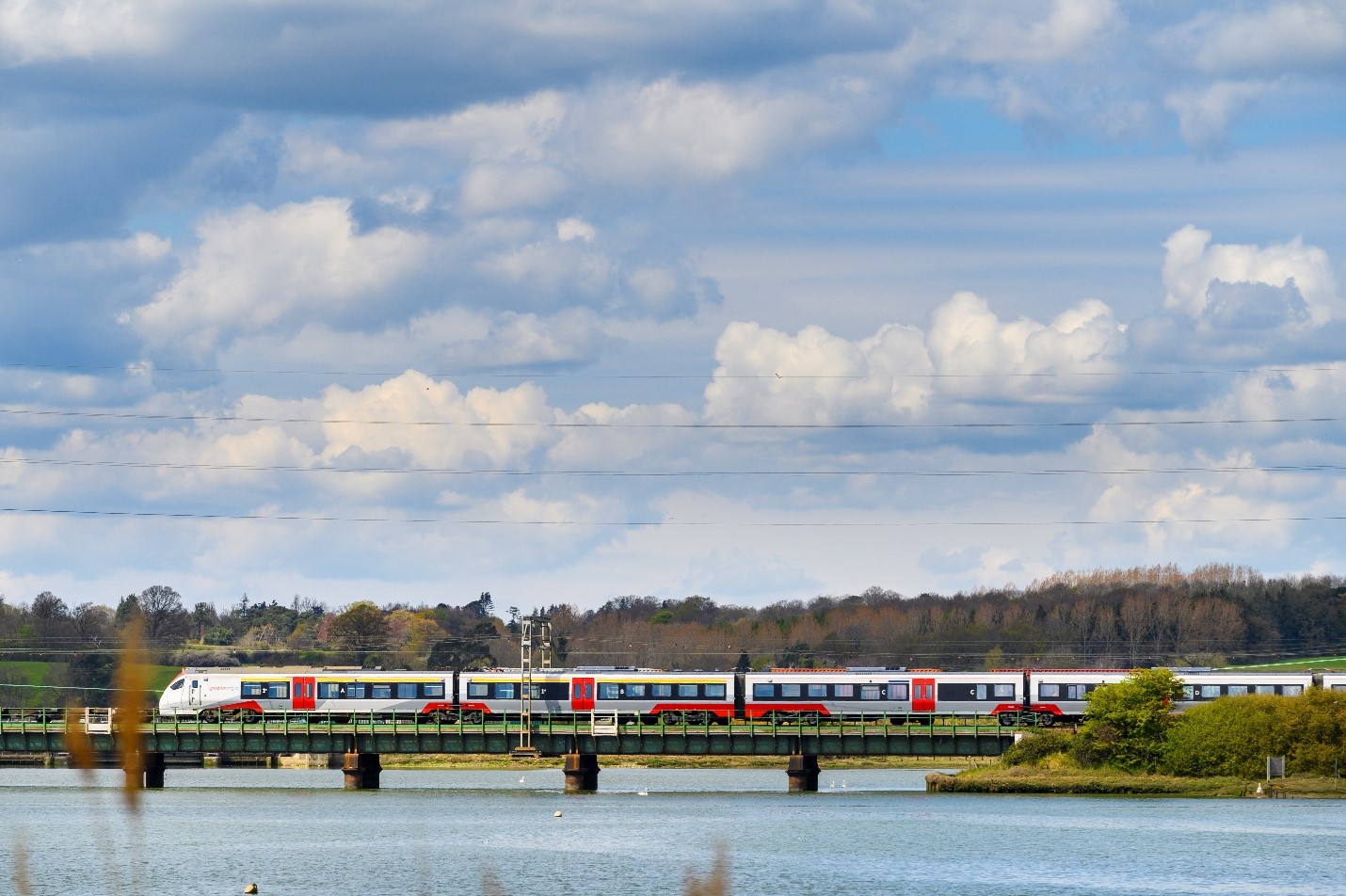