Key messages:
- in 2023 to 2024 we have continued to emphasise the importance of a proportionate safety management system in what are challenging times for the sector, by publishing new guidance in this area. Incidents that we have investigated throughout the year have frequently been linked to a failure by operators to manage change safely.
- our interactions within the sector in 2023 to 2024 included inspections focusing on work at height, and general health and safety inspections of railways. The output of these inspections has assisted us in developing an overall assessment of maturity of the sector’s management of health and safety using RM3. This assessment is similar to previous years with the majority of criteria considered to be “managed”. One criterion, change management, is less mature than in 2022 to 2023 based on the evidence sampled this year. There remains significant potential for a more standardised approach to be adopted by the sector and we continue to engage with industry groups to achieve this. We remain of the view that a dedicated body to draft and publish guidance and standards for the heritage sector can help deliver this.
Figure 5: Heritage and Minor Railways 2023 to 2024 RM3 Assessment
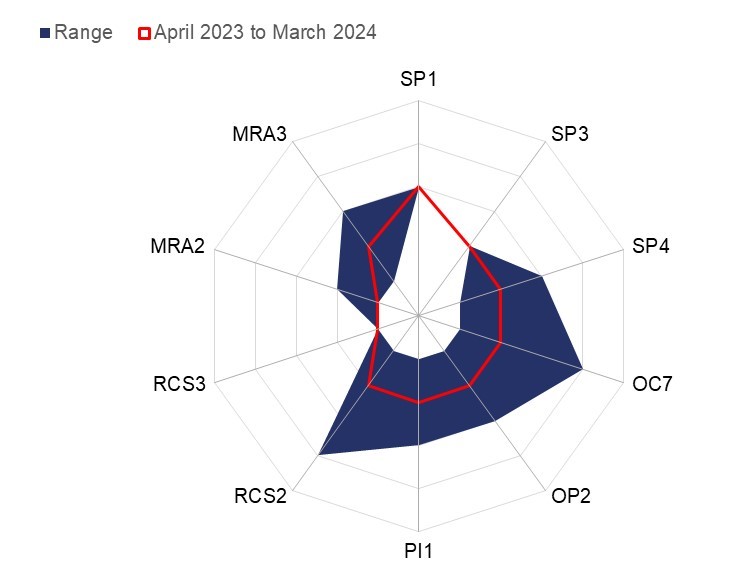
Source: ORR
Table 2: Heritage and Minor Railways 2023 to 2024 RM3 Assessment
Code | Description | 2023 to 2024 Assessed Level | Min | Max |
---|---|---|---|---|
SP1 | Leadership | 3 | 3 | 3 |
SP3 | Board Governance | 2 | 2 | 2 |
SP4 | Written Safety Management System | 2 | 1 | 3 |
OC7 | Record Keeping, Document Control and Knowledge Management | 2 | 1 | 4 |
OP2 | Competence Management System | 2 | 1 | 3 |
PI1 | Risk Assessment and Management | 2 | 1 | 3 |
RCS2 | Management of Assets | 2 | 1 | 4 |
RCS3 | Change Management | 1 | 1 | 1 |
MRA2 | Audit | 1 | 1 | 2 |
MRA3 | Incident Investigation | 2 | 1 | 3 |
Source: ORR
In August 2023 we published new sector specific guidance on safety management systems. We strongly believe a systematic approach to health and safety management can ensure that operators meet relevant legislative requirements and operate in a safe manner. We have reinforced this through a series of industry workshops (see case study below).
In 2023 to 2024 we served three Improvement Notices on heritage and minor railways. Two of those notices were served following a failure by the railway to safely manage a change to their operations, highlighting the importance of identifying changes and ensuring any impacts on safety are assessed and managed. The other notice related to the management of operational staff competence.
Our investigation into a fall from height at the Gwili Railway Company Ltd. in 2022 concluded this year with a decision to prosecute the railway. The railway pleaded guilty and was subsequently fined £18,000 in September 2023.
Analysis of incidents reported to us indicates that the number of derailment incidents increased during 2023 to 2024 (12 in total). The majority of these incidents (10) occurred at narrow gauge railways and arose for a variety of reasons including the track asset, the vehicle and the actions of operational workers.
Fortunately, the majority of these incidents occurred at low speed and did not result in any injuries, however the increase is concerning and in different circumstances these incidents could result in harm.
In 2024 to 2025, we plan to undertake inspection activity in the specific areas of work at height, asbestos management, and on-track plant, as well as undertaking some general inspections of a sample of railways. We will also continue to engage railways through face-to-face workshops to drive improvements in safety management system capability across the heritage sector.
Case Study 5: New Safety Management System Guidance for the Heritage and Minor Railway Sector
In August 2023, ORR published new guidance for heritage and minor railways. This document was developed as we have consistently found weaknesses in the safety management systems of these railways and have served several improvement notices in recent years related to this.
The document provides a summary of requirements within the Railway and Guided Transport Systems (Safety) Regulations 2006 (ROGS) for safety management systems and how duty holders may apply these requirements to their own railway. The document recognises the diversity of operators that exists within the sector and recommends a proportionate approach.
We ran a series of face-to-face workshops in collaboration with the Heritage Railway Association (HRA) in January and February 2024 to promote the new guidance at locations across Great Britain. Representatives from 82 railways and tramways attended these workshops.
Case study 6: Work at Height Inspections
In 2022 and 2023 there were several incidents at heritage railways whereby a volunteer, contractor or member of staff was seriously injured as a result of a fall from height. In response to this adverse trend, ORR undertook specific and targeted inspections on the management of work from height at nine heritage railways in 2023 to 2024.
Our inspections found some common areas of weakness. Risk assessment was the most prominent area of weakness with often a failure to consider all the tasks undertaken at height and identify appropriate control measures. Many control measures identified in risk assessments were often only briefly described and open to interpretation. Some railways failed to ensure work at height equipment was maintained in a suitable condition. Fundamentally there was often limited monitoring and audit associated with work at height practices meaning operators had not identified their own weaknesses.
However, we saw several examples of good practice, for example:
- various measures to reduce the risk associated with emptying locomotive smokeboxes ranging from bespoke working platforms to undertake the task safely to self-cleaning fireboxes to reduce the frequency at which the task is undertaken.
- adaptation and redesign of watering equipment both on and off the locomotive to minimise working at height, for example low-level water filling of tenders
- secure Ladder guards on work at height equipment in publicly accessible areas e.g. signal post ladders on station platforms.
- bespoke guarding on carriage doors undergoing maintenance and restoration to prevent falls from height in a workshop environment.
- comprehensive asset registers for work at height equipment.
In summary, our inspection findings indicate that the sector is not always meeting minimum legal requirements when undertaking work at height and there is scope for the sector to improve. Operators should start with ensuring a suitable and sufficient risk assessment is in place appropriate for the work being undertaken. Railways then need to ensure that the measures identified through risk assessment are implemented and ensure that there are appropriate measures in place to check that these measures are effective.