What is a Fatigue Risk Management System?
5.1 A Fatigue Risk Management System (FRMS) is a more formalised arrangement for controlling fatigue than the basic controls described in section 4. Although a FRMS can include all employees, it would be used by organisations whose staff are likely to: carry out safety critical work; work long hours from time to time; work significant overtime; carry out shift work; use potentially dangerous machinery at work; work near moving vehicles/construction plant; work at height; carry out electrical work.
5.2 A FRMS identifies and draws together all the preventive and protective measures which help an organisation control risks from fatigue. It should be based on a comprehensive understanding of fatigue, managing fatigue in a flexible way which is appropriate to the size, risk and nature of the operation. An FRMS should so far as is reasonably practicable:
- Be based on sound fatigue control principles rather than custom and practice.
- Take account of fatigue information collected about the organisation’s own operations and feedback from staff, tailoring fatigue controls accordingly.
- Be integrated with the company Safety Management Systems (SMS).
- Be a continuous and adaptive process, continuously monitoring and managing fatigue risk, whatever its causes.
5.3 A Department for Transport study (Fourie and others, 2010b) reported several advantages of adopting a FRMS approach, including improved safety, improved staff morale, reduced absenteeism, competitive advantage, and futureproofing against any changes in legislation.
Integrating the FRMS with wider risk control systems
5.4 An effective FRMS should be integrated with the organisation’s wider Safety Management Systems (SMS). Under ROGS 2006 Regulations 5 and 6, all operators and dutyholders are required to have in place arrangements for managing safety risks and monitoring the performance of their safety system, known as a Safety Management System. A SMS should be adapted to fit the size and nature of the operation.
5.5 The building blocks of the FRMS will be an extension of existing processes for managing safety. For example, existing incident-reporting forms may only need slight expansion to collect information for fatigue analysis. Data should flow freely between the general SMS and the FRMS, which should use similar processes (Fourie and others, 2010b). So, although the term Fatigue Risk Management System could imply a stand-alone or discrete system, in practice most elements of the FRMS should be integrated with the company’s other risk control procedures. A document could be used to signpost to existing fatigue controls and allow any gaps to be identified.
A proportionate approach to managing risks from fatigue
5.6 Organisations should design an FRMS to fit their own operation and avoid using a generic system. An organisation’s FRMS should be tailored to its own operations and context, proportionate to their size, complexity, and degree of fatigue risk, with substantial involvement and input from staff. To determine the likely scope of controls needed and the rigour of controls required, an assessment should be made of the degree of exposure to risk from fatigue in the operation. Then:
- If likely risks from fatigue are assessed as relatively low (e.g. only daytime work; no safety critical tasks performed) simple arrangements such as those outlined in section 4 ‘Basic fatigue controls’ may suffice, and it may only be necessary for a single person to oversee the fatigue management arrangements.
- At the other end of the scale, if staff work shifts, there is significant overtime and especially if they carry out safety critical work, likely risks from fatigue could be relatively high, warranting more rigorous controls and a comprehensive FRMS (Fourie and others, 2010a). Suggested key components are outlined in the remainder of this section.
Fatigue Risk Management Systems – The Plan, Do, Check, Act approach
5.7 There is no ‘one-size-fits-all’ for fatigue risk management systems, and in reality, the various fatigue controls will usually be embedded in the organisation’s over-arching risk management systems rather than existing as a separate system. The HSE publication HSG65 ‘Managing for health and safety’ outlines the Plan, Do, Check, Act approach. This approach helps to achieve a balance between the systems and behavioural aspects of management; it treats health and safety management as an integral part of good management generally, rather than as a stand-alone system. The Plan, Do, Check, Act cycle should not be seen as a once only action and organisations should adopt the cyclical approach to managing their health and safety risks, particularly when starting out, developing a new process, or implementing any change. This cycle is illustrated in Figure 5.1.
Figure 5.1 The Plan, Do, Check, Act cycle for managing fatigue
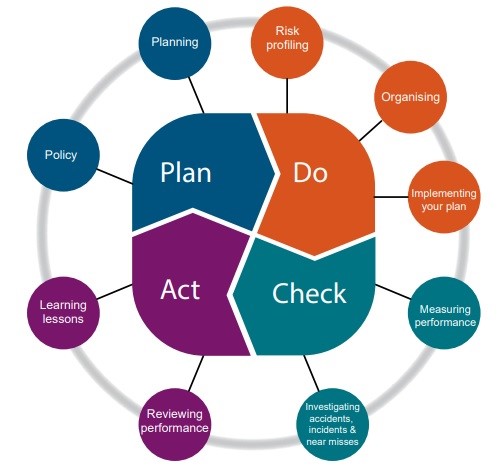
Source: Reproduced from HSE. Graphic licensed under the Open Government Licence v3.0 and subject to HSE’s copyright statement.
5.8 Although other approaches can be used, the same general principles outlined in the Plan, Do, Check, Act cycle can be found in most effective management systems, including Fatigue Risk Management Systems. Guidance on applying the Plan, Do, Check, Act approach to fatigue management is provided in sections 6 to 9 inclusive. In especially complex situations, and where fatigue risks could be high, it may be prudent to seek advice from a competent professional with expertise in assessing and managing fatigue.